Interview 2: Teia, a Sheet Metal Worker
Teia is a fabricator with Sheet Metal Workers Local 292 in Detroit, MI
Women Who Weld, a 501(c)(3) nonprofit organization that teaches women how to weld and find employment in the welding industry, has launched a new program - Arclight - in which we showcase women who create, ideate, and collaborate across specializations and trades.
Teia Leonard completed Women Who Weld’s Intensive Welding Training Program in October 2019 and landed a job as a production welder at a custom steel packaging company. After working as a production welder for just short of a year, Teia became a fabricator with Sheet Metal Workers Local 292 in Detroit, MI. Below is an edited and condensed interview between Samantha Farrugia, the founder of Women Who Weld, and Teia, a former Women Who Weld participant, in January 2021.
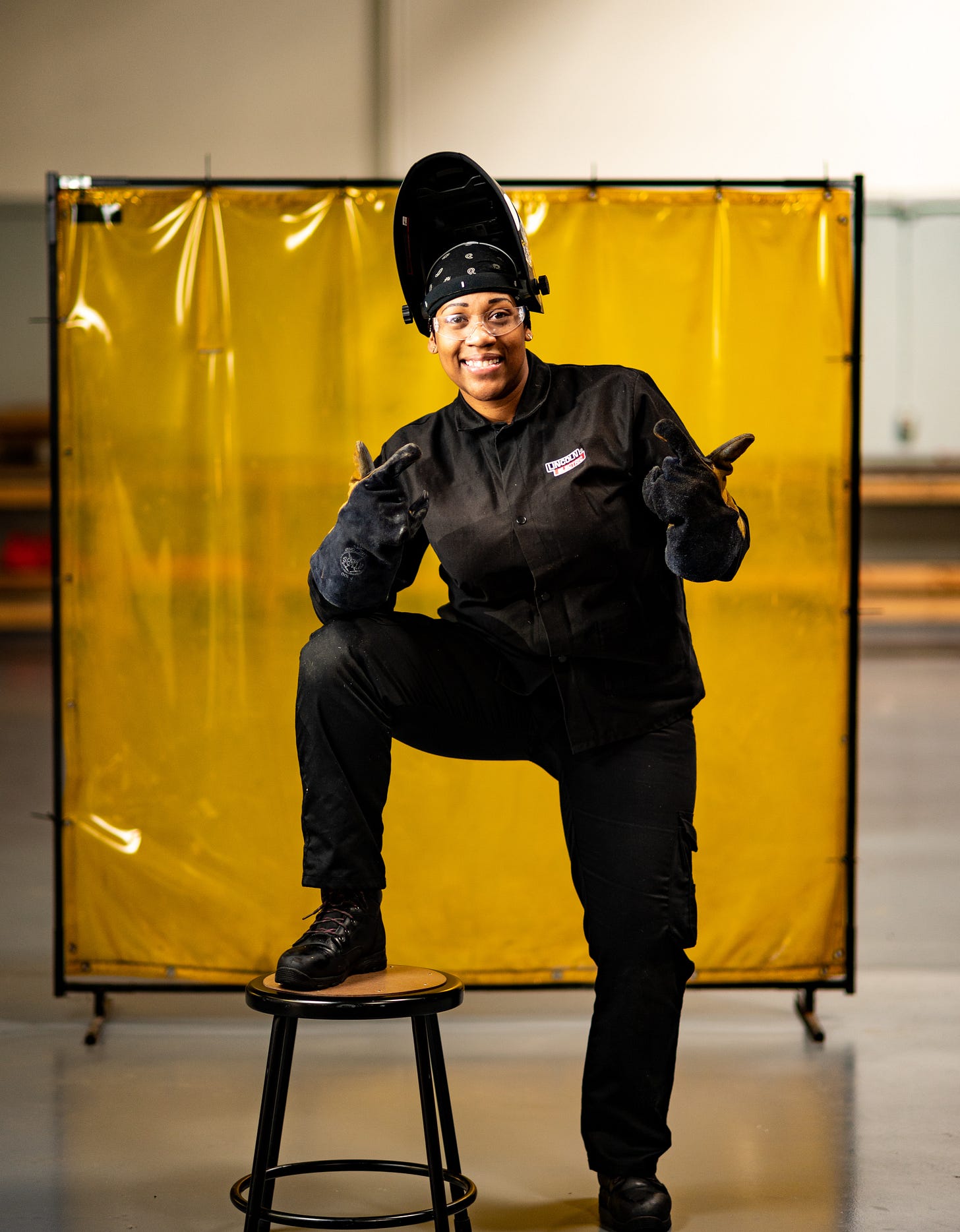
Before you went through Women Who Weld’s intensive welding training program, you were a press machine operator at a stamping plant. What was that job like and what did you do there?
I did spot welding there. It was very robotic. Essentially, I just swiped a button. We built car parts for GM and Toyota.
When you were attending Women Who Weld’s training program each day from 9:30 a.m. - 2:30 p.m., you would leave promptly at 2:30 p.m. to race to the stamping plant to work the second-shift. What were your hours at that job?
My shift was 3 p.m. until about 2 in the morning.
Did you find it challenging to go through Women Who Weld’s fast-paced training in which you have to take in a lot of new information to learn a new skill, and study each night for the daily tests we administer, while also working full-time as a press machine operator?
My god, yes! But it helped me understand what I was doing at the stamping plant a little better, like how the machines work; I don't think all of my co-workers paid attention to that. At my former job I saw this guy welding and I was like, “Wow, he's not swiping a button,” and he had his music going and a leather jacket on, he was super cool. And I thought, “I could do that.”
There are so many different types of welding, not just spot welding, and going through the program helped me understand this. But, oh my god, going through the program and working that job while on my feet all day was exhausting.
Women Who Weld’s intensive welding training program is intensive, we pack a lot of information and training into a relatively short period of time. Our program is designed to enable participants to learn a new skill fast; we distill information and technique in a way that makes welding accessible, fun, and interesting to learn. Would you agree?
Yes, I think the way it was presented helped everyone retain information better. I tell people all the time that my instructors at Women Who Weld equipped me with more than just the basics of welding. I find myself a lot of times – which makes me super proud – pointing out things a lot of the old heads don't even know. Many people learn the trade as they go, but you often find they're doing things wrong. You guys did such an awesome job with making sure we understood things. That is what makes Women Who Weld stand out, and that's what makes me stand out anywhere I go because I know what I'm talking about.
Before you worked in manufacturing, you were in a totally different industry, working as the head chef for a school district. Why did you leave the food industry for manufacturing?
I've always wanted to work in manufacturing, I just love that atmosphere. I'm a tomboy and I don't mind getting dirty, and I love being able to hang with the guys, so the kitchen was never going to be me for long. I love to cook, but it makes me feel good to know I can do what men do, and do it a little bit better. And when I got the opportunity to work at the stamping plant, I was like, “Okay, this is a foot in the door.” I knew of welding but I didn't understand everything related to it and thought, “Okay, I'll be here for like a year or two.” They had a really dope apprenticeship at the stamping plant, but it wasn’t until after I got hired that I found out they don't really afford those opportunities to women, so I was kind of stuck.
When I’m engaging participants, I often use cooking analogies because there are many parallels between welding and cooking. In both you’re often dealing with exact measurements and hot items; adjusting the heat to get the best outcome; and listening for a particular ‘sizzle’ just as you listen for particular sounds when cooking on a stovetop.
That is crazy, they seem very different but yes, they're similar! I did not put that together until you just said it. In both environments you are loading and unloading items, and my welder is like my oven and I have to know when to adjust the heat!
After you completed Women Who Weld and left your job at the stamping plant, you landed a job as a production welder. What was that job like and how does it differ from your current job as a sheet metal worker?
There is no comparison. My current job is more hands-on and much more detailed. My previous job was basic production welding; you’re given parts and you weld them. When we had reviews, I would tell my former supervisors that if we were given a little more responsibility, we would understand more and create a more efficient product. We weren't even responsible for measurements and the machines were already set for us. I call it being a lazy welder; the machine is already set, so you just turn it on, put two pieces in a jig, weld it, and call it a day. So you don't get as much experience. Especially being a woman, they kind of relegate you to certain things. There’s no comparison to the things I do now as a sheet metal worker.
For example, where I work now there are different machines and most don't display the numbers, you're just working with knobs on the face of the machine. So, I had to learn how to do that all over again, trying to find the right amperage and voltage, set my wire speed, and figure out what settings work for what I'm welding. Because it's not the same for everyone, it's what you feel comfortable with based on your travel speed and work angle. You are left to figure out the machine for yourself.
Production welding is often about quantity over quality. In fabrication, you take your time to get it done the right way. No one is rushing you, you know, as long as you're moving. You can take time to study the blueprint, you get time to understand what you’re doing. There's a lot more focus.
Do you refer to yourself as a welder or a fabricator? Or do you say you're a welder/fabricator?
I am a fabricator. For people who don't understand, I tell them a fabricator’s job is more detailed; it’s when you get into blueprints and understand how to create shapes, it's more custom. We build specifically to what the client wants.
Do you feel production welding was a good first step in the industry as a welder?
We learned so much through Women Who Weld and I didn't feel like I was applying all of that knowledge as a production welder. Though being a production welder gets you comfortable with welding because you're welding every day. And that's the difference with fabrication: welding is a big part of being a fabricator, but there's so much more you need to know, and that's when I really apply everything I learned from Women Who Weld.
There are several trade unions engaged in welding, including the Boilermakers, Carpenters, Ironworkers, Millwrights, Pipefitters/Steamfitters, Sheet Metal Workers, and so on. Why did you choose to join the Sheet Metal Workers union?
After finishing Women Who Weld, I felt like an apprenticeship was the natural next step and I initially wanted to do the Pipefitters apprenticeship training program but they weren’t accepting applicants at the time. So, I took a job as a production welder, which helped me slow down a bit and weigh my options.
But after about 6 months as a production welder, the pandemic struck and I was feeling stuck at my job. I was super bummed because I felt like I was too skilled to be in this one spot. But I didn't want to hurry and pick a union at that point. So, I ended up testing to be a b-rate welder for the Sheet Metal Workers union. And when I showed up for my weld test and saw what they were doing, I was like, “Wow, they're up high, this place looks so big, and it looks so complicated.” And it was interesting to see them building these structures. I thought, “I could do this, I could stay here for a bit until I figure out exactly what I want to do.” And then I just fell in love with sheet metal.
And for those who are unfamiliar, union Sheet Metal Workers belong to The International Association of Sheet Metal, Air, Rail, and Transportation workers, known by the acronym SMART. Members of SMART’s Sheet Metal Division fabricate, assemble, weld, install, and repair sheet metal products and equipment. Further, sheet metal workers are employed across a range of industries such as automotive, rail, transportation, aviation, and boat and ship building, and engage in architectural work as well as systems and equipment within buildings, including refrigeration, HVAC, ductwork, and so on.
Sheet Metal Workers Local 292 has a unique focus: its members specifically handle the manufacturing and installation of automotive and industrial paint finishing systems. What exactly is your role in making these systems and what time does your workday start?
I work the graveyard shift from 5:30 p.m. until 4 a.m.
I read blueprints, weld, operate cranes, and make installations. I build automotive paint finishing systems, including industrial burner ovens, that are installed in automotive plants. Industrial burner ovens are part of the paint finishing system. The burner oven essentially cooks the paint on vehicles, and when the oven heats up, the metal on the vehicle expands to allow the heat - from the heating system we built - to cook the paint on properly. And huge vehicles have to fit inside these ovens that I’m building! There is a lot of electrical to know, so I’m learning so much, it’s really cool.
I also install ductwork for the paint finishing system and that involves a lot of welding. After I weld the ducts, which are huge – sometimes like 60 feet tall – I use a crane to lift the ducts into the finishing system. I build and install walls, which I first have to insulate. I then crane these walls in to create the frame of the system. I also build the rails to support the walls that I crane in.
There is a lot of cutting and grinding with sheet metal, and the grinding infuriates me because I create these perfect welds and then I make them disappear! But, depending on which parts I am working on, I might not be doing much welding. There is much more to know than just welding; I’m building, it’s like construction with only metal.
Which welding processes are you using at work?
I MIG weld, usually in short-circuit, and sometimes in spray transfer. I also just started welding flux-cored.
For those who don’t know, MIG, which stands for Metal Inert Gas, also known as GMAW, which stands for Gas Metal Arc Welding – as this process often involves an inert and reactive shielding gas, a mixture of 75% Argon and 25% CO2, for example – is a welding process in which a machine feeds gas and wire (the electrode) through a protective cable and out the tip of a welding torch controlled by the welder. It’s a versatile welding process used commonly in industrial fabrication and repair, and, unlike stick welding, is generally performed indoors as MIG/GMAW requires still air to not affect the gas that is shielding the weld. Additionally, short-circuit and spray are different types of metal transfer: the way in which small droplets of metal literally transfer across the electric arc that is created between the welding torch and the metal being welded on. Short-circuit and spray transfer require different gas mixtures and machine settings, and serve different functions. In spray transfer, metal droplets spray across the arc similar to holding your thumb over a garden hose; welds are deposited very hot and very fast, so spray transfer is often used in high-volume production. In short-circuit transfer, a small molten droplet forms at the tip of the electrode, falls, and shorts the electrical circuit between the machine and base metal several hundred times a second; welds are thus deposited a bit cooler and slower compared to spray transfer, but no less effective and penetrative with the right technique.
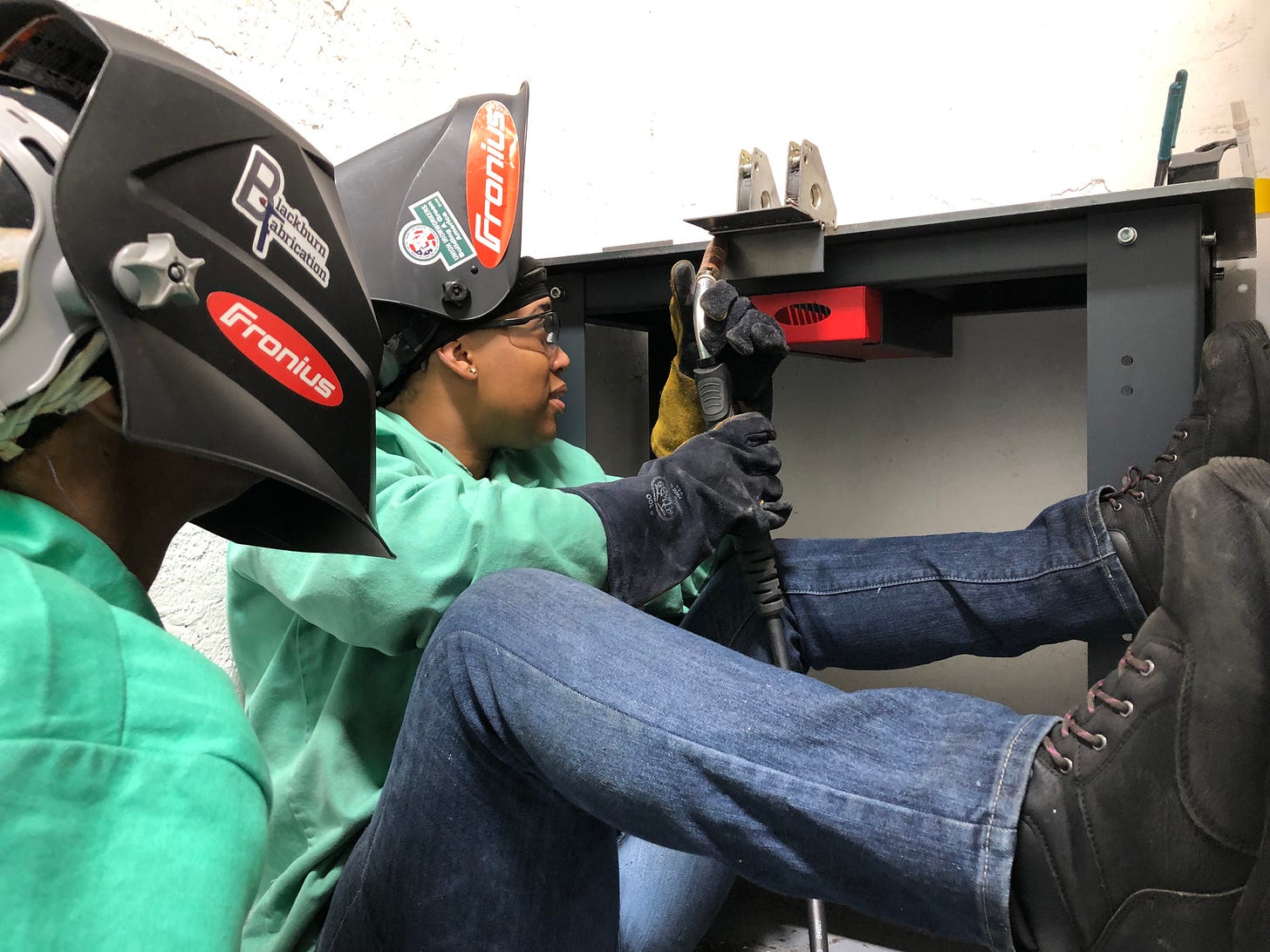
What range of metal thickness are you typically working with?
The thickest metal I’ve worked with is quarter inch (1/4”), and that’s for when I build the bases. I’ve worked on 16 gauge (1/16”) and thinner, which is normally what most of the ductwork is made of, but when it’s that thin, I tack weld it.
You’re a member of Sheet Metal Workers Local 292 and considered a b-rate welder, which means you have to pass a challenging weld test to get hired. Only about 50% of people who take this weld test pass. Tell me about the weld test, and how you passed?
Oh my god, that test was hard; it was very challenging. But I put together what I learned through Women Who Weld’s training, and welding every day as a production welder. When you take the test, and when you're familiar with the angles and joints they ask you to do, and you understand what your work angle and travel speed should be, it's easier. It then just comes down to setting your machine and figuring out your speed in the moment.
They have you weld a t-joint and a lap joint, but they really look for that corner edge joint; and they want to know you can run a stringer because that's important when you're dealing with thin metals. They want the welds to be flush, so flush it's not even there. And before my test I was thinking, “They like it hot, so don't try to go too fast, don't make it too convex…” After laying these stringers, I thought, “Oh my god, my toes aren't straight!” And the guy overseeing the test says, “You say you've never done sheet metal before?” I'm like, “No…”, and he says, “Wow, that's pretty frickin’ perfect; for what you're working on, this is as straight as you’re going to get these toes because this is galvanized. I don't even need to see anything else, we'll call you”. And I walked out of there feeling like, “Wow…I just did that!”
How does a b-rate welder compare to being a sheet metal apprentice or journeyworker?
The main difference between a b-rate welder and sheet metal apprentice is the title, and that is why I was interested in becoming a b-rate welder; I knew I didn't have to immediately jump into an apprenticeship, that I could come in as a b-rate welder which means you know what you're doing and the pay is nice. You just don't have certifications yet. If you're an apprentice, you are not delegated better work or more work, we're all just working together. Though you might see a difference if someone is a journeyman. They have more privilege and they'll do most of the welding on sensitive parts.
Also, the bosses are always watching, and if they see that you know what you're doing, you’re going to get more responsibility. But you kind of have to have thick skin working in these places, because when we're trying to get things done, not everyone is going to talk to you in the nicest way, and it's up to you to decide what is disrespectful or understand what just needs to be done when they are throwing out orders. You have to be willing to learn, willing to listen, and you have to discern between what’s right and wrong.
It was my first week on the job as a sheet metal worker and I was instructed to weld ductwork for the first time. When I arrived at work the next day, my foreman said, “The bosses are super impressed with your work.” And it just made me feel like everything I had been working so hard for, all the meals I missed to get to training on time, was worth it.
“That is what makes Women Who Weld stand out, and that's what makes me stand out anywhere I go because I know what I'm talking about.”
What is your weekly schedule like?
We are supposed to start at 5 p.m., but due to Covid, they try to make sure there's not a lot of traffic, so we start about 5:30 p.m. and our shift ends at 4 a.m., Monday through Friday. On Saturday and Sunday, I go in at 3:30 p.m. and get off at 12 a.m.
Wow, so you're working seven days a week?
Sundays aren't mandatory, they are afforded to you if you work Monday through Saturday. Working on a Sunday amounts to like $400 in overtime. Working any shift after Thursday, though, is considered overtime, so you're making time and a half – and you get addicted to the overtime. Technically you don’t have to call in on Saturdays, but you don’t want to make a habit of it. So, I take a Saturday off only if I have to. I’ll take a day off to not have a day off, because then it’s my day to clean, grocery shop, and prep my son’s meals through the week as well as my lunch for the week.
Do you like working nights? And if so, why?
I have always worked nights. I'm a mom so I really appreciate being able to be there during the day. Prior to Covid, I could drop my son off at school and if anything happens, I'm available. I'm a night owl and I don't mind sleeping during the day. I appreciate working nights, especially now with Covid. The night shift is a tighter crew, so there's not a lot of people, and I would say that we do most of the fabrication.
Because you work nights, I’m curious to know what your routine is like? When you do sleep? When do you eat?
I eat breakfast around four in the afternoon. Then I have a break at work around 8:30 p.m. and I'll just snack a little bit. I'm diabetic so I try to eat as healthy as I can. We have our lunch break at 11:30 p.m. On my way home, I grab dinner from a drive-thru because who’s cooking at 4 in the morning? I get home just after 4:30 a.m., and I eat, then shower, and try to get some sleep for a few hours before I have to get up and make sure my son is ready and in school online at 8:30 a.m. Then I take another little nap and get up to check on my son and then nap again. My schedule is weird, it’s so weird, but you get used to it.
You’re a single-mother with a demanding work schedule and you work nights. This alone is a lot to manage, but I’m sure it’s made even more challenging by the pandemic. How old is your son? If he is attending school remotely at home, how do you watch him if you also need to sleep?
My son is 6, he will be 7 next month. My mom lives with me but she is sick with chronic kidney failure. I live across the street from my sister, so she’ll help out. I'm very proud of the way I’ve raised my son because he's very self-sufficient and independent. I prep all his meals and he's reading now, so I'll leave him notes telling him how long to warm his food, and notes with the time he has to take a shower and be in bed by. But it’s so tough to try to give him quality time and I do feel bad at times because, you know, he's knocking on the door like, “Can I come in?” and I’m like, “I’m sleeping!” But Sundays are our days, I just make it about him. And he can't wait for it, he loves it.
He told me the other day, “You work so hard to get us all the monies.” He understands what I’m doing and why I’m doing it. And I tell him, “This is part of growing up, I can’t be with you all the time.” And, fortunately, his schoolwork does not suffer because of it; he is a straight-A student and he’s reading at a third-grade level. So, it’s working out.
Does he think it’s cool that his mom is a welder?
Yeah, he would ask me what I do and I would explain it to him and then we would watch welding videos together, and he’s like, “That’s so cool!” He gets it, he loves it. He told his teacher, “My mom’s a welder, she plays with fire all day!”
Your income has doubled in the last year since you’ve become a welder. How has welding improved your financial stability and personal mobility?
It definitely allows me to save more. I've always been super frugal and tied to a budget. I had emptied my savings a couple times in the past, and it's nice to have savings to fall back on now. And it's nice to be able to create a safety net for my son. That's what this increase does for me, and I know it's coming every week. But I'm still on a budget, so I don't think about the money I save; I don't see it, I don't need it. In the long term, it will be nice to be able to purchase a home and that's what we're planning for soon. I don’t want to rent anymore. If I’m going to spend all this money, I'd rather put it toward a mortgage.
Women constitute 5% of welders and, according to data from the U.S. Bureau of Labor Statistics, only 3.3% of sheet metal workers in the United States. Do you have advice for women who may be interested in pursuing a path in sheet metal working or welding?
Frickin’ do it! But you have to have thick skin. You have to really think about if this is something you want to do. As with anything you do, your skill set and attention to detail will be the difference.
In welding, and especially in sheet metal, there are not a lot of women, there’s only two of us during my shift. And I find that sometimes women in this industry are not friendly toward one another. You know, like, most of us are too busy doing the tough girl act, right? But you have to talk to one another, support one another because that is what is missing. It is very hard and we’re scarce in this industry, but you just have to focus and not be afraid to ask questions. Don't be afraid to Google. Don’t be afraid to learn and figure out how to take your time. If you don't know, ask. If you're scared to ask, this is not for you.
What are your future career aspirations?
I am applying for the Sheet Metal Worker apprenticeship training program in April. I want to become an apprentice and I want my journeyman’s card. I feel like that is the only thing stopping me from being the greatest welder ever. If you have your certs, you get more responsibility; and I want to supervise and lead.
If you weren’t a welder/fabricator/sheet metal worker, which career path may you have chosen?
I definitely would have stuck with my career as a wedding singer. I don't have stage fright, but I hate attention and I feel embarrassed when people focus on me. And I had to get to a place, especially after my divorce, where it was okay for people to see that I can't dim my light.
“I want to become an apprentice and I want my journeyman’s card. I feel like that is the only thing stopping me from being the greatest welder ever.”
If you could travel anywhere, where would you go and why?
That’s such a tough question for me. It took me forever to realize there are places outside of Michigan, like, I knew there were places outside of Michigan, but that I could go to those places. And I was also scared to fly anywhere. I’ve been on a plane one time, a few years ago, and it was a one-hour flight to Atlanta.
But, I would go to the Bahamas because I’ve never been to a beach, ever! I’ll be 30 years old in April, which is also when I’m getting married. So, we’re hitting the beach for our honeymoon!