Interview 18: Elizabeth, a Sheet Metal Worker
Elizabeth is a Journeyworker with the Sheet Metal Workers in Detroit, MI
Arclight is a long-form interview series in which Women Who Weld, a 501(c)(3) nonprofit organization that teaches women how to weld and find employment in the welding industry, showcases women who create, ideate, and collaborate across specializations and trades.
Elizabeth Schweitzer completed Women Who Weld’s Intensive Welding Training Program in October 2018. Elizabeth holds a bachelor’s degree in interior design from the College of Creative Studies and she is now a journeyworker with Sheet Metal Workers Local 80 in Detroit, Michigan. Below is an edited and condensed interview between Samantha Farrugia, the founder of Women Who Weld, and Elizabeth, a former Women Who Weld participant, in March 2024.
Where are you calling from?
From home in Pontiac, Michigan.
Where did you grow up?
Lapeer, Michigan.
Where did you work before becoming a sheet metal worker?
I’ve had multiple jobs. I was in retail sales, I did staffing for a creative group, and I was an interior designer.
Why did you decide to leave your interior design career and pursue welding?
I was actually in a sales job after working in interior design. I was looking to make a move and get more into my creative side. I wanted to learn more and get deeper into jewelry soldering, as well as welding and sculpture welding. When I talked to a friend of mine, she recommended Women Who Weld and said, “They teach you how to MIG weld and help you find a career where you weld and fabricate.”
When did you become an apprentice with Sheet Metal Workers Local 80?
I took the entry test in January 2019. I believe 165 people took the test and they interviewed the top 30, and out of the top 30 they took the top 15, and I made the cut!
That’s great! There are several trade unions engaged in welding, including the Boilermakers, Carpenters, Ironworkers, Millwrights, Pipefitters/Steamfitters, Sheet Metal Workers, and so on. Why did you choose to become an apprentice with the Sheet Metal Workers?
During my time as a participant of Women Who Weld, we visited the Local 80 training facility and they talked about using Revit and AutoCAD software to develop the BIM (build information modeling) drawings, or blueprints, for sheet metal, and having journeymen actually produce the drawings. They mentioned they mostly deal with soldering when installing copper roofing for their architectural projects, but they also have a heavier welding side in which they stick or MIG weld on-site or in a shop. They engage in so many different things, some of which I had some knowledge of, and it seemed like it would be a good fit for me.

Tell me about Local 80’s architectural division.
Local 80 has an architectural section and an HVAC section. I started out in architectural because I wanted to climb up on roofs to solder and do some of the architectural work on the exterior of buildings, but it wasn’t a good fit for me physically. I switched to HVAC which is a better fit for me. I get to work indoors most of the time, so I’m not always out in the cold; though there are many days where I’m still outside in the dead of winter and I have on insulated bibs and toe and hand warmers. It's not always cushy and warm in the wintertime, it just depends on the job that you're working.
And Local 80 has a lot of people using AutoCAD and Revit for the blueprints and BIM drawings. And that’s really what my goal is within the local: I want to move into a detailing position. The best detailers in our trade work in the field first so that they really understand sheet metal before going into the office and just detailing.
The more drawings I examine on-site when installing ducts, the easier it is for me to understand how to be a better detailer. It’s helpful to see what good detailers do and also what bad detailers do. The biggest lesson for me was realizing that someone might be very good at using the software, but if they don’t know anything about working with sheet metal, then they are not a good detailer because they don’t understand how things are fabricated or installed. When that’s the case, a lot of the guys, or women, in the field have to figure out how to make it work and it feels like having to do the impossible sometimes! At that point, it gets complicated since the BIM drawings have been created and approved; they've done some sort of checking with the other trades to make sure it doesn't interfere with the pipe fitters or the plumbers or the electricians. Many things have to come together. It all has to be cohesive on really big projects.
For some of the smaller projects, sometimes it's a build-to-design. A lot of projects in schools don't necessarily have an exact drawing; there is a general idea and then it's up to the foreman to figure out the exact materials, the gauge, and the depth they want to use. It’s then up to the journeyworkers to put it up in the air.
Were there other women in your apprenticeship cohort? Do you ever work with other women?
There are a few women in our local, it's around 1%. We have a little over 1,000 members; the number sort of changes and fluctuates as apprentices enter and journeymen retire.
I’ve also worked with women in other trades, like plumbers, pipefitters, electricians, and ironworkers. There were quite a few women on the roof of the new JLA tower in Detroit doing rod busting. I’ve also worked with female laborers, general contractors, and heads of safety.
You’re now a journeyworker with the Sheet Metal Workers. How long was your apprenticeship?
It was supposed to be five years when I joined, but my class and the classes before and after mine received two six-month bumps to move it to four years because there was so much work and just not enough journeyworkers. So they keep bringing in new classes of apprentices and turning out journeymen in order to have enough manpower for jobs we have in Michigan, but also to send to companies down in Tennessee and Kentucky where they’re working on a chip plant. These are big, big jobs, and the unions aren’t very strong down south and they don't have a lot of manpower down there, so they're taking people from other locals with a lot of workers to choose from.
When exactly did you become an apprentice?
April 1, 2019 was my first day on the job. I spent the week before my first day at the training center, and the instructors gave us a heads up like, “Hey, this is what this tool is called; this is what you're going to be working on; this is what you guys are going to be doing.” We were pre-apprentices and a lot of people came in with no knowledge.
I did lose some time working, as well as training in school, because of Covid; it affected a lot of the time we actually had to learn. And for me, coming from such a different background and not knowing much about the trades or construction other than just doing floor plans in AutoCAD or Revit or some 3D modeling for interior design, I wanted to have as much experience as possible as an apprentice before turning out. But the more you do it, the more you try, the more questions you ask, and the more you keep trying, you start to understand a lot more than you ever did. I surprise myself all the time by just trying certain things I've never done before and doing it, figuring out how to do something that needs to be done.
That’s great to hear. It’s like a daily or weekly challenge for yourself.
Oh, daily, haha, daily!
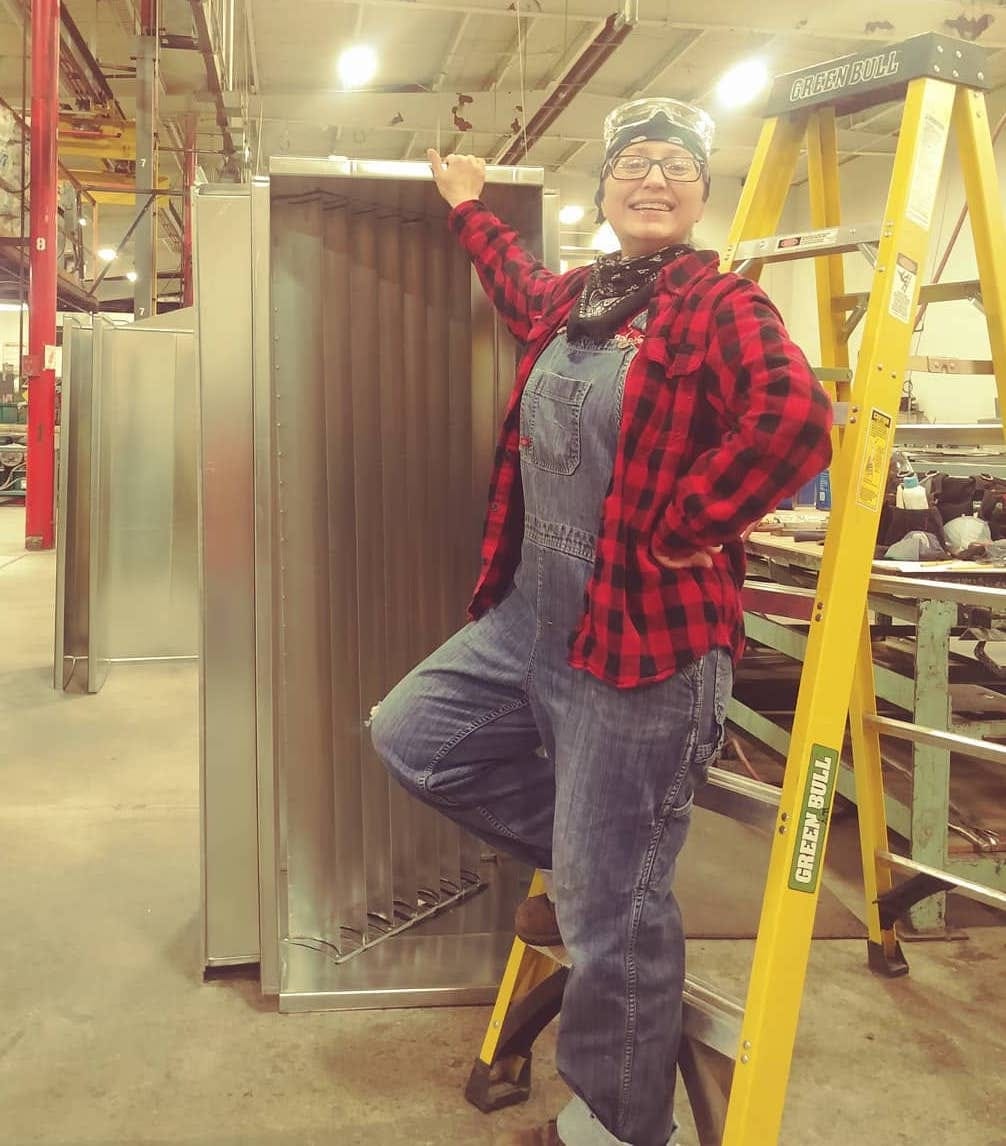
What has changed in your role from apprentice to journeyworker? Was there an immediate change or was it incremental?
I'd say incremental change naturally. When I actually received journeyworker status as of July 1, 2023, I had already been working on the same job, a school project. I'd been doing the same thing before and continued to do so after. But at the same time, you do get more responsibility and you're supposed to step up to the plate more. Still, when I'm doing something, or about to do something, or somebody asked me to do something I haven't done before, I will ask a question just to make sure I know what I'm about to do; this way I have a better idea of what the foreman expects of me.
Where do you currently work and when did you start working there?
I’m at Danboise Mechanical, which is the smallest company I’ve worked at and I started in December 2023.
Are you working on a specific project for them?
We tend to have multiple jobs going at the same time for their sheet metal division, so the projects are not the type I go to every day for six months, day after day. I jump around a lot. I’ll work on projects in Belleville, in Centerline, in Fraser, in Royal Oak.
We’re working on a big project for an elementary school in a very old building. I’m also working on a project for a cell phone company to update some of their ductwork to help keep their systems cool. For another company, in a big warehouse containing their servers, we’re also updating the HVAC system to keep their equipment cool. And when we’re doing an install, everything is brand new from the shop.
I’ll demo, update systems, do new installs; it varies. Some of the buildings are very old and some of the buildings are a lot newer.
What’s your schedule like, including start and end time, each day? Which days of the week do you work?
Monday through Friday from 7 a.m. to about 3:15-3:30 p.m., our regular hours. We get a break in the morning and we get a break at lunch. Sometimes you can start at 6 a.m. and get out a little earlier, and you'd have the same break mid-morning and at lunch. It depends on the job and the foremen and when you can get into the building or on site to start your work. I'm often starting at 7 a.m. but on Monday we have a job and the start time is 6:30 a.m.
Can you describe a typical day on the job?
On a day when I'm replacing ductwork, the old ductwork gets removed and then a new unit gets put on the roof or inside the building. We completely remove the old ductwork from the ceiling, down to the top of the unit so there's no ductwork left. Then another trade will come in and remove the old unit, and we might go to another job site while they do that. We’ll go back the next day or whenever we get our ductwork to reinstall. My foreman has to draw out all of the fittings and pieces: detailing how tall, how wide, how deep; if it’s going to have a transition; if it’s just a straight piece, things like that. Then we install and connect it.
When I was working on the Book Depository building in Detroit for Ford, or the University of Michigan’s new hospital, we would get truckloads of ductwork multiple times a week, and we would have to be on a deck to receive the duct. There were also other sheet metal workers down below, taking the duct off the truck, rigging it and placing it on the crane; the crane would lift it all the way up to the floor you're on. It was huge duct!
What other companies have you worked for and what projects have you worked on?
I started my apprenticeship at C.A.S.S. Sheet Metal where I installed exterior sheet metal panels and vertical metal panels at the new Wayne County Community College building. Then I worked at Conti and installed new AC units in classrooms and tied in new ductwork to existing ductwork for a school district. I then worked at Limbach in the detailing/B.I.M. department for the new Wayne County Criminal Justice Complex courthouse; I also made the ductwork in the shop then installed it at the courthouse. After that project, I worked at Conti on Ford’s Book Depository duct system. I then worked at Ainsworth on the ductwork for the new JLA Apartments in Detroit, and then went back to Conti to work on ductwork for Livonia Public Schools. And, mostly recently, I worked with Applegate on the Dan and Betty Khan Health Pavilion at the University of Michigan.
I like doing big jobs because it's really cool to see all the material going in, especially with new construction. But I also enjoy working at small companies, because the jobs are a bit unique and the ductwork is smaller, which I like because I'm about five feet tall so it's a little easier for me to deal with. If I’m on a two-person crew, smaller ductwork is easier to carry if there is no elevator.
What is your hourly pay?
On my check, before taxes, it is $41.29 and, on top of that, my package includes health insurance, vision, dental, and my pension. So, in total, I believe my employer winds up paying almost $80 per hour for me to work. We also get vacation pay for every hour we work; my employer sends my vacation pay to the local and they deposit it into a bank account of my choice.
Are you earning more money now as a sheet metal worker than as an interior designer?
Oh yeah, definitely. 100%
How often did you attend classes as an apprentice?
Our program is different and I wish they would change it, and I think they're trying to work out a better system, but they front-load most of the information in the first year of the apprenticeship, so we're in school a lot our first year. Personally, I was not able to take and sort out all of the information that was crammed into my head the first year.
The other trades go to school once a week or once every two weeks, and I like that system more because it allows you to digest and understand everything while working in the field. Whereas it was page after page after page after book after book after test after test after test. We had lab classes, but I feel there's only so much you can do in school; the majority of the training has to be on the job. It was really hard for me to learn the way we did, because everything was thrown at us at once and it was just too much for me, which, I think, does a disservice to someone like me who didn't grow up welding and working on cars in the garage with my grandpa, learning these mechanical fields. All of which would suit me right now, but I had absolutely no idea when I was playing with Barbies inside the house, and my grandpa was out in his garage working on his cars, that I would need some of that information now. And I never, never would have wanted to get dirty or get my dress dirty back then or even 10 years ago! I couldn't even imagine doing this job.
And now you’re dirty every day?
Oh, yeah, definitely. But, with the way our economy is and the student loan debt crisis that so many people are suffering from, myself included, I had to do something because I was not making enough money to pay my student loan debt and try to have all the things you're supposed to have when you become an adult, you know?
Do you mind disclosing how much student debt you currently have?
I believe I'm somewhere around $120,000. I've been paying on it since I graduated in 2010. I had a few periods of deferment during Covid where I didn't have to pay and they weren't charging interest. My student loan payments every month alone are at least $1,000.
When I see other apprentices, who are 18 and just getting into the trade, I’m like, “You are so smart and so lucky. You're going to turn out; you're going to be able to buy a new truck, a new house, you're going to be living the dream.” In my opinion, unless your parents are wealthy, or unless you go for a STEM career, college is just way too expensive for the majority of people. They're shrinking the middle class; they want everyone to be poor and starving, or extremely wealthy. And honestly, even with the money I'm making now, with the rise in cost of everything, I'm still not exactly where I want to be. And there are layoffs and slow times, and everyone is talking about another 2008 crash. I think it could happen, and it’s going to affect Michigan, and it's going to affect me and everyone in my local and in the construction industry. Projects will go on pause and they’ll have to lay people off.
But, if I were in a position where I didn't have student loan debt, I would be doing so much better; it would be amazing. I'm basically paying on a mortgage without having my own house.
When you are constructing and installing these HVAC systems, are you welding them?
No, because I usually use slip and drive ducts that fit together when hammered, or TDF and TDC flange connections, which I tighten down with bolts and nuts or lag bolts. And then I use duct sealer to seal the connections so air doesn’t escape.
Most members in my local who weld do so in the shop. Or, with what I’m doing, the HVAC side of installs, there might be a shaft duct that runs through the building to the unit on the roof and it also connects the ducts on every floor, and it needs to be fastened securely so that it doesn’t shift or move. For example, when I worked on the Ford Book Depository, there was nothing in the shafts that we could connect to, we had to build and create a support structure for the duct to hang off of. And this happens in a lot of shaft work: we drill through the cement and use angle iron to secure it and bolt it down, and oftentimes you have to weld some of the angle iron together inside the shaft if it is really heavy duct. Or you might drill holes in the angle iron to connect it to. It just depends on the foreman and the duct and the application and the standards.
So, when you are welding, what’s your favorite welding process and why?
I really like MIG welding, it’s one of my favorites. I did some stick welding in school. It was so hard, so frustrating, but I definitely want to try it some more. I also like oxy-acetylene. It reminds me of jewelry soldering. I also like the hiss from the gas, there's something soothing about the noise and even the smell.
What sort of tools and equipment do you use regularly?
Sheet metal hammer, snips, vise grip, handle lock, duct pullers, clip tool, level, screwdriver, 5/16” attachment for my impact driver, ratchet wrench. There’s a lot in my bag, it’s full of stuff!
What are your future career goals?
I would like to work in the field for maybe 5 to 10 years and get really good at what I'm doing, and then make a transition into detailing.
What do you like most about being a sheet metal worker?
I love learning things I never even knew existed before. It's a new world so often for me. Learning how to do things that not everybody knows how to do; how to use tools that not everybody knows how to use; and how to problem solve things that were once sort of mystifying, like, “How did they do that? How was this done? How was it built?” Being able to see everything built from the ground up alongside other trades like the pipefitters, plumbers, and electricians, and seeing everything they do. It's helped me to become a self-sufficient, can-do kind of handy woman around the house. I never ever would have attempted to do a ton of the things I've done until I got into the trade.
Do you have advice for women who may be interested in pursuing a path in sheet metal work?
I don’t mean this in a bad way, but I don't think the trades are for soft women. I am a soft woman who has had to be very, very strong and that's how I’m able to be in this type of environment.
It’s not just women though, think about all the men who would not survive doing this type of work.
Absolutely. And I don't just mean physically, that's part of it, but I'm talking about mentally, emotionally, physically, spiritually, because there are some people who will absolutely try to break you down.
There are a lot of people who are there for you and support you, and they're wonderful, but when you have to move and jump around a lot, you don't always get to stay with the same team of people. I've met a lot of people who I really, really liked and I would love to still be working with. But every once in a while, you run into people, either in your trade or in another trade and they just ruin your day, or ruin your self-esteem, or just bring all that negative bad energy. And this can happen anywhere in any type of job or any office work, but it’s almost worse when you're the only woman in a buck hoist filled with men.
What do you like to do in your free time?
I don't really have a whole lot of free time. The schedule I have to keep is very strict. I wake up very early for work, anywhere from 3:30 to 4 in the morning, because most of the time I have at least an hour drive and I have to pack a lunch and feed my cats. So, when I get home from work, it's just shower, take care of the animals, do some cleaning, do some laundry. On the weekends I just want to chill and relax; sometimes I like to go out for a hike. In the summertime I love to go to the beach to go swimming. I love going up north. I love to travel. I love doing spiritual witchy things with crystals and incense. I love going to art galleries and art openings. I like going to live music shows. But, again, a lot of that is limited due to my work schedule. And I’m getting older, I’m tired!
If you were not a sheet metal worker, which career path may you have chosen?
I probably would have stuck with interior design, interior design sales, or possibly just gotten more into the mystical, spiritual, esoteric side of things.
If you could travel anywhere, where would you go and why?
I would go to Ibiza because I would love to go dancing at all the clubs and hang out on the beach!